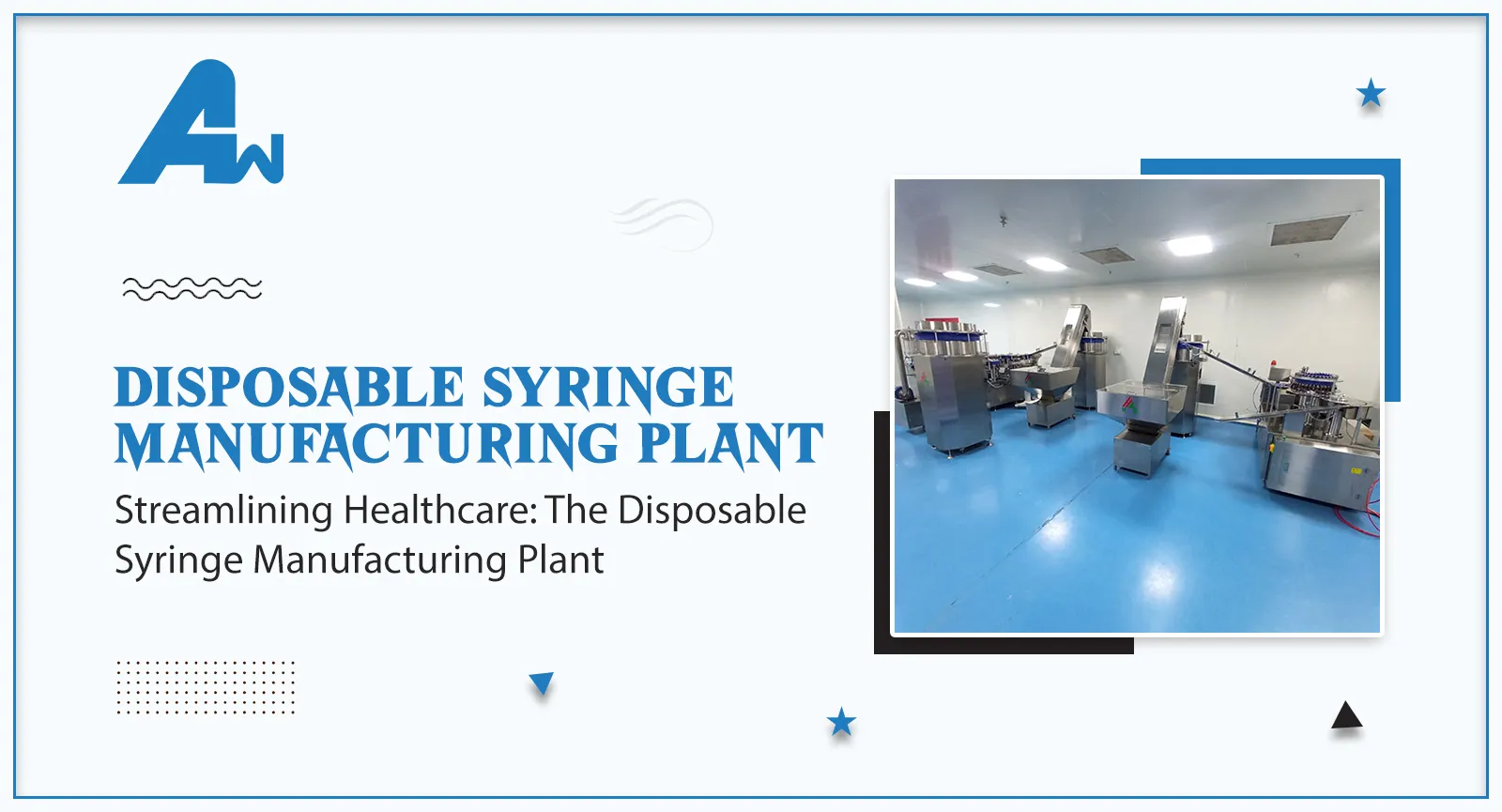
In healthcare, one indispensable tool that revolutionised medical practices is the disposable syringe. These simple yet powerful devices have significantly prevented infections, administered medications, and improved patient care. Behind the scenes, a remarkable feat of engineering and manufacturing takes place to ensure a steady supply of these vital instruments.
In this blog, we will explore the intricate workings of a Disposable Syringe Manufacturing Plant, shedding light on the key processes involved and the impact they have on global healthcare.
Design and Development:
The journey of a disposable syringe begins with meticulous design and development. Engineers work closely with medical professionals to create syringes that meet stringent safety standards, ensuring optimal functionality and user-friendly features. Advanced computer-aided design (CAD) software is employed to model the syringe’s shape, dimensions, and mechanisms accurately. The design process also incorporates features like barrel capacity, needle compatibility, and secure luer lock systems.
Raw Materials and Quality Control:
Manufacturing high-quality disposable syringe making machine necessitates the careful selection of raw materials. Medical-grade polypropylene or polycarbonate polymers are chosen for their durability, transparency, and biocompatibility. The raw materials undergo rigorous testing to ensure they meet the required standards for strength, chemical resistance, and absence of contaminants.
Automated vision systems and quality inspectors perform regular checks, monitoring various parameters such as dimensions, leak resistance, needle sharpness, and compatibility. Compliance with international regulatory standards, such as ISO 13485 and FDA guidelines, is of utmost importance to guarantee the safety and reliability of the syringes.
Injection Molding :
The injection molding process is the heart of Disposable Syringe Manufacturing Plant suppliers in India It involves the precise and automated production of syringe components. The raw polymer material is heated, melted, and injected into a mould cavity with the desired syringe barrel and plunger shape. Cooling and solidification follow, allowing the mould to be opened and the newly formed component to be ejected. This process ensures consistent production with minimal variation.
Injection moulding machines in a syringe manufacturing plant can operate continuously, producing large quantities of syringe barrels and plungers. The moulds used are designed to be highly efficient, allowing for rapid production cycles and minimal wastage. After the components are moulded, they move on to the assembly stage.
Assembly and Packaging :
The assembly of a disposable syringe involves bringing together the moulded barrel, plunger, and needle. Specialized automated machines perform this task with precision and speed. The barrel and plunger are ultrasonically welded or heat-staked together, ensuring a secure bond. The needle, made of stainless steel or other medical-grade alloys, is attached using various methods, including adhesive bonding or press-fitting.
Once the syringes are assembled, they undergo final inspections to guarantee adherence to quality standards. Then, they are packaged in sterile and tamper-proof containers, ensuring that they remain uncontaminated until they reach end-users. The packaging process typically involves blister packs or sealed pouches, clearly labelled with essential information such as product details, lot numbers, and expiration dates.
Sterilization:
Ensuring the sterility of disposable syringes is of utmost importance in healthcare settings. Manufacturing plants employ various sterilization techniques to eliminate any potential microbial contamination. Common methods include ethylene oxide (EtO) gas sterilization, gamma irradiation, or autoclaving. These processes effectively destroy microorganisms while maintaining the structural integrity of the syringes. Sterilization validation and monitoring are crucial aspects of the manufacturing process, with regular tests conducted to confirm the effectiveness of the sterilization methods.
Environmental Considerations:
Disposable syringe-making plants are increasingly adopting environmentally conscious practices. Efforts are made to minimize waste generation through optimized production techniques, efficient material usage, and recycling initiatives. Recycling systems are implemented to reprocess and reuse excess or defective syringe components, reducing overall environmental impact. Additionally, energy-efficient machinery and technologies are utilized to minimize energy consumption and greenhouse gas emissions.
Automation and Advanced Technologies:
Disposable syringe-making plants are increasingly adopting automation and leveraging advanced technologies to enhance production efficiency and ensure quality control. Robotics, machine learning, and artificial intelligence are utilized to automate tasks such as assembly, inspection, and packaging. These cutting-edge technologies enable higher production rates, improved precision, and cost reduction. Real-time monitoring and data analytics systems are implemented to track manufacturing metrics, identify bottlenecks, and optimize processes for continuous improvement.
Conclusion:
The Disposable Syringe Manufacturing Plant Manufacturers in India play a crucial role in meeting the ever-increasing demand for safe and reliable medical instruments. By combining advanced technology, stringent quality control, and automated processes, these plants ensure the production of high-quality syringes that help protect patients and healthcare providers worldwide.
As we continue to strive for advancements in healthcare, Allied Way India has become one of the leading companies in the manufacturing industry and will continue to innovate and refine its processes to enhance patient safety and contribute to the overall well-being of society.
Related Posts
Write the difference between a Cannula and needles.
When it comes to the medical industry, both needles and stainless steel cannula play a…
Understanding the Features of Water Tank Making Machines
A water tank is an efficient means of storing water. Having the right water tank…
How to Start Manufacturing Disposable Syringes with Needles?
The healthcare industry is booming and starting the business for disposable syringes with needles can…
Essential Features of High-Quality HDPE Blow Moulding Machine for Water Tank
If you are involved in manufacturing water tanks, getting a high-quality HDPE blow moulding machine…